基于单元型巷道的超前液压支架装置的制作方法
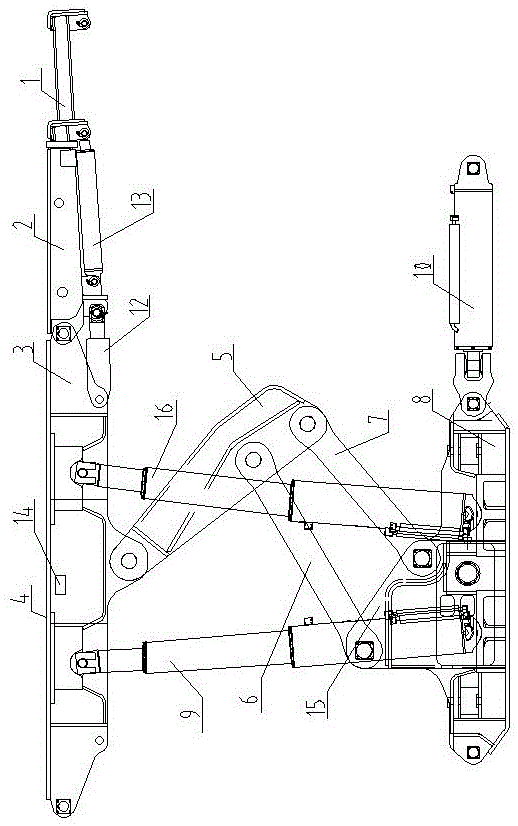
本实用新型涉及一种超前液压支架装置,尤其是一种基于单元型巷道的超前液压支架装置。
背景技术:
单元型巷道的超前液压支架装置作为煤矿的支护装置,被广泛的应用,因此基于单元型巷道的超前液压支架装置是一种重要的矿山装置,在现有的基于单元型巷道的超前液压支架装置中,巷道超前支护液压支架普遍采取的是步进式顶梁支护顶板,这种支撑方法虽然简单方便易操作,对顶板支撑力大,能有效支撑顶板,但这种支护方式会反复支撑顶板,不利于对顶板的安全管理和维护,易造成顶板的破碎,对井下巷道工作人员生命及设备造成威胁,同时,安装、维护、拆卸这种支架时工作人员劳动强度非常大,用人多并且回柱危险性强。
基于现有的技术问题、技术特征和技术效果,做出本实用新型的申请技术方案。
技术实现要素:
本实用新型的客体是一种基于单元型巷道的超前液压支架装置。
为了克服上述技术缺点,本实用新型的目的是提供一种基于单元型巷道的超前液压支架装置,因此提高了超前液压支架装置的可靠性能。
为达到上述目的,本实用新型采取的技术方案是:包含有设置在支护点的地基上的底座、设置在支护点的顶面上的支撑板装置、设置在底座和支撑板装置之间并且相邻的两个伸缩立柱之间的夹角设置为19-23°的伸缩立柱组。
由于设计了底座、支撑板装置和伸缩立柱组,通过底座,形成地面支撑,通过支撑板装置,形成顶面支撑,通过伸缩立柱组的伸缩立柱的伸缩量的调节,对支撑板装置的位置进行复位调节,防止顶面支撑出现偏移,不再使用单个的伸缩立柱,因此提高了超前液压支架装置的可靠性能。
本实用新型设计了,按照形成前后平衡支撑点的方式把用于地面支撑的底座、用于顶面支撑的支撑板装置和具有至少两个伸缩立柱的伸缩立柱组相互联接。
本实用新型设计了,按照沿底座的竖向中心线向外倾斜的方式把伸缩立柱组与底座和支撑板装置联接。
本实用新型设计了,还包含有推移伸缩缸、斜梁、上连杆、下连杆和立柱护板,支撑板装置设置为包含有伸缩梁、前梁、顶梁、护顶板、前梁伸缩缸、推动伸缩缸和护顶伸缩缸,伸缩立柱组设置为包含有左伸缩立柱和右伸缩立柱,
在顶梁和底座之间设置有左伸缩立柱和右伸缩立柱并且在底座的侧面部上设置有立柱护板,在立柱护板上设置有上连杆和下连杆并且在顶梁和上连杆之间、顶梁和下连杆之间设置有斜梁,在底座的端头设置有推移伸缩缸,在顶梁的侧面部设置有护顶板并且在顶梁与护顶板之间设置有护顶伸缩缸,在顶梁的前端端面部设置有前梁并且在顶梁与前梁之间设置有前梁伸缩缸,在前梁的前端端面部设置有伸缩梁并且在前梁与伸缩梁之间设置有推动伸缩缸。
本实用新型设计了,顶梁设置为包含有箱部、左连接耳和右连接耳并且左连接耳和右连接耳分别设置为与箱部的端头联接,在箱部的底端端面部分别设置有左销轴孔和右销轴孔并且在左连接耳和右连接耳上分别设置有插孔体和铰接孔,左销轴孔设置为与左伸缩立柱联接并且右销轴孔设置为与右伸缩立柱联接,插孔体设置为与前梁联接并且铰接孔设置为与前梁伸缩缸联接,护顶板和护顶伸缩缸分别设置为与箱部的侧面部转动式联接,箱部设置为矩形箱状体并且左连接耳和右连接耳分别设置为双耳状体,左销轴孔、右销轴孔、插孔体和铰接孔分别设置为圆形孔并且左销轴孔和右销轴孔分别设置为沉入在箱部中。
本实用新型设计了,底座设置为船形体并且底座设置为包含有底板部、左后侧板部和右前侧板部,在底板部的侧面部的左端部分别设置有左后侧板部并且在底板部的侧面部的右端部分别设置有右前侧板部,在左后侧板部和右前侧板部之间设置有立柱护板并且右伸缩立柱和推移伸缩缸分别设置为与右前侧板部铰接式联接,底板部设置为U字形板状体并且底板部的左右端头设置为向上呈锐角延伸分布,左后侧板部的端头和右前侧板部的端头分别设置为具有向外延伸的拐角板状体。
本实用新型设计了,立柱护板设置为直角梯形板状体并且在立柱护板上分别设置有左连接孔、右上连接孔和右下连接孔,左连接孔设置为与上连杆联接并且右上连接孔设置为与下连杆联接,立柱护板设置为镶嵌在底座中并且左连接孔、右上连接孔和右下连接孔分别设置为圆形孔,左伸缩立柱设置为与立柱护板铰接式联接。
本实用新型设计了,左伸缩立柱和右伸缩立柱设置为三节式伸缩缸并且左伸缩立柱的上端端头的转动轴和右伸缩立柱的上端端头的转动轴分别设置为与顶梁串接式联接并且左伸缩立柱的下端端头的转动轴和右伸缩立柱的下端端头的转动轴分别设置为与底座联接,左伸缩立柱的竖向中心线与右伸缩立柱的竖向中心线之间的夹角设置为19-23°,左伸缩立柱的竖向中心线与底座的竖向中心线之间的夹角设置为8-10°并且右伸缩立柱的竖向中心线与底座的竖向中心线之间的夹角设置为11-13°,左伸缩立柱和右伸缩立柱分别设置为沿顶梁的横向中心线间隔排列分布。
本实用新型设计了,斜梁设置为梯形板状体并且在斜梁的前端头设置有第一铰接孔部,在斜梁的后端头设置有第二铰接孔部和第三铰接孔部并且第二铰接孔部和第三铰接孔部设置为呈间隔排列分布,第一铰接孔部设置为与顶梁联接并且第二铰接孔部设置为与上连杆联接,第三铰接孔部设置为与下连杆联接,第一铰接孔部、第二铰接孔部和第三铰接孔部分别设置为圆形孔。
本实用新型设计了,上连杆和下连杆分别设置为矩形条状体并且上连杆的一个端头和下连杆的一个端头分别设置为与立柱护板铰接式联接,上连杆的另一个端头和下连杆的另一个端头分别设置为与斜梁铰接式联接并且上连杆与下连杆设置为呈相互平行排列分布。
本实用新型设计了,推移伸缩缸设置为两节式伸缩缸并且推移伸缩缸设置为通过连接钩与底座联接。
本实用新型设计了,前梁设置为箱状体并且在前梁的左端头设置有连接耳部,在前梁的右端头设置有容纳腔体并且伸缩梁设置在前梁的容纳腔体中,前梁的连接耳部设置为与顶梁联接并且前梁伸缩缸设置为与前梁的下端端面部联接。
本实用新型设计了,伸缩梁设置为矩形板状体并且在伸缩梁的中间部设置有连接耳部,伸缩梁设置为与前梁插接式联接并且推动伸缩缸设置为与伸缩梁的连接耳部铰接式联接。
本实用新型设计了,护顶板设置为矩形板状体并且护顶板设置为通过销轴与顶梁翻转式联接,护顶伸缩缸设置为与护顶板的下端端面部铰接式联接。
本实用新型设计了,前梁伸缩缸、推动伸缩缸和护顶伸缩缸分别设置为两节式伸缩缸,前梁伸缩缸的一个端头设置为通过销轴与顶梁联接并且前梁伸缩缸的另一个端头设置为通过销轴与前梁联接,推动伸缩缸的一个端头设置为通过销轴与前梁联接并且推动伸缩缸的另一个端头设置为通过销轴与伸缩梁联接,护顶伸缩缸的一个端头设置为通过销轴与顶梁联接并且护顶伸缩缸的另一个端头设置为通过销轴与护顶板联接。
本实用新型设计了,顶梁和底座与左伸缩立柱和右伸缩立柱设置为按照呈V字形支撑的方式分布并且顶梁、底座、左伸缩立柱和右伸缩立柱与立柱护板、斜梁、上连杆和下连杆设置为按照侧支撑护栏的方式分布,顶梁与伸缩梁、前梁、护顶板、前梁伸缩缸、推动伸缩缸和护顶伸缩缸设置为按照全方位扩展延伸的方式分布并且伸缩梁的中心线、前梁中心线、顶梁中心线、底座中心线、前梁伸缩缸中心线和推动伸缩缸中心线设置在同一条直线上,一个立柱护板、一个斜梁、一个上连杆和一个下连杆设置为组成一组侧支撑护栏部件并且两组侧支撑护栏部件分别设置在顶梁和底座之间的侧面部。
本实用新型设计了,还包含有横向连接头和连架收缩缸并且横向连接头的一个端头设置为与底座联接,连架收缩缸设置在相邻的两个横向连接头的另一个端头之间。
本实用新型设计了,在横向连接头的一个端头设置有通孔部并且在横向连接头的另一个端头设置有叉口部,横向连接头的通孔部设置为通过销轴与底座铰接式联接并且横向连接头的叉口部设置为通过销轴与连架收缩缸铰接式联接,横向连接头设置为沿底座的横向中心线间隔排列分布。
本实用新型设计了,连架收缩缸设置为具有双头伸缩部的三节伸缩缸并且连架收缩缸的伸缩头设置为通过销轴与横向连接头联接。
本实用新型设计了,还包含有竖向连接头和连架收缩缸并且竖向连接头的一个端头设置为与顶梁联接,连架收缩缸设置在相邻的两个竖向连接头的另一个端头之间并且连接头的另一个端头设置为与左伸缩立柱的上端端头联接。
本实用新型设计了,在竖向连接头的端头分别设置有通孔部并且竖向连接头的上端端头的通孔部分别设置为通过销轴与顶梁铰接式联接,竖向连接头的下端端头的通孔部分别设置为通过销轴与左伸缩立柱和连架收缩缸铰接式联接,竖向连接头设置为沿顶梁的横向中心线间隔排列分布。
本实用新型设计了,连架收缩缸设置为具有双头伸缩部的三节伸缩缸并且连架收缩缸的伸缩头设置为通过销轴与竖向连接头联接。
本实用新型的技术效果在于:采用板式结构,斜梁、连杆分布支架中间两侧,立柱分布支架整体中间两端,形成水平双三角形结构,保证了支架的稳定性,为整组超前支架具有良好的稳定性和运动轨迹提供保证。单架采用窄型四连杆机构,加大空间,降低风阻面积,更加有利于矿井通风,保证井下通风质量,底座为整体式刚性底座,底座前后部采用厚钢板船式结构,具有排矸防扎底功能,底座中部直接与连杆连接,形成四连杆机构,提高整体支架抗扭矩作用,两侧设计侧翻梁,对两侧煤壁进行支护,为行人空间提供安全保护,防止侧面煤壁出现片帮和冒顶中间采用多级侧翻梁,可实现护顶面积大,支护能力强等优点,具有安全、稳定的特点,顶梁、底座均计支架复位调节机构,提高支架抗偏载能力,通过液压千斤顶复位调节并列支架位置,提高支护整体稳定性,单元型支架体积更小,移动更方便灵活,迈进式移架改变了传统超前支架的的移架方式,连杆采用高强材质板式结构,采用立柱居中,连杆偏移的三角布置结构,具有更强的稳定性,减小支架支护端面,对顶支护强度更大,高效快速的顶板支护,更利于人员和设备的安全保障,新增支架复位机构,提高支架抗偏载、抗水平能力,该单元型巷道超前液压支架的应用,可明显减少井下超前支架移架作业人员2人,移架时间由原来的平均45分钟减少到平均30分钟,不仅为用户节省了人员成本,而且生产效率提高了1/3,开采量显著提高,移架方式的改变,提高了推移效率,减少了支架反复支撑次数,更加有利于减缓支架磨损,与以往矿方使用一年支架后需更换立柱数量相比,该单元型巷道超前液压支架的立柱损坏大大降低,重复使用次数和使用寿命明显改善。
在本技术方案中,形成前后平衡支撑点的底座、支撑板装置和伸缩立柱组为重要技术特征,在基于单元型巷道的超前液压支架装置的技术领域中,具有新颖性、创造性和实用性,在本技术方案中的术语都是可以用本技术领域中的专利文献进行解释和理解。
附图说明
为了更清楚地说明本实用新型实施例或现有技术中的技术方案,下面将对实施例或现有技术描述中所需要使用的附图作简单地介绍,显而易见地,下面描述中的附图仅仅是本实用新型的一些实施例,对于本领域普通技术人员来讲,在不付出创造性劳动的前提下,还可以根据这些附图获得其他的附图。
图1为本实用新型的第一个实施例的示意图;
图2为本实用新型的顶梁3、斜梁5、底座8和立柱护板15的连接关系示意图;
图3为本实用新型的第二个实施例的示意图;
图4为本实用新型的第三个实施例的示意图;
1-伸缩梁、2-前梁、3-顶梁、4-护顶板、5-斜梁、6-上连杆、7-下连杆、8-底座、9-左伸缩立柱、10-推移伸缩缸、16-右伸缩立柱、12-前梁伸缩缸、13-推动伸缩缸、14-护顶伸缩缸、15-立柱护板、41-横向连接头、18-竖向连接头、11-连架收缩缸。
具体实施方式
根据审查指南,对本实用新型所使用的诸如“具有”、“包含”以及“包括”术语应当理解为不配出一个或多个其它元件或其组合的存在或添加。
在本实用新型的描述中,需要说明的是,术语“中心”、“上”、“下”、“左”、“右”、“竖直”、“水平”、“内”、“外”等指示的方位或位置关系为基于附图所示的方位或位置关系,仅是为了便于描述本实用新型和简化描述,而不是指示或暗示所指的装置或元件必须具有特定的方位、以特定的方位构造和操作,因此不能理解为对本实用新型的限制。此外,术语“第一”、“第二”、“第三”仅用于描述目的,而不能理解为指示或暗示相对重要性。
在本实用新型的描述中,需要说明的是,除非另有明确的规定和限定,术语“安装”、“相连”、“连接”应做广义理解,例如,可以是固定连接,也可以是可拆卸连接,或一体地连接;可以是机械连接,也可以是电连接;可以是直接相连,也可以通过中间媒介间接相连,可以是两个元件内部的连通。对于本领域的普通技术人员而言,可以具体情况理解上述术语在本实用新型中的具体含义。
此外,下面所描述的本实用新型不同实施方式中所涉及的技术特征只要彼此之间未构成冲突就可以相互结合。
下面将结合本实用新型实施例中的附图,对本实用新型实施例中的技术方案进行清楚、完整地描述,显然,所描述的实施例仅仅是本实用新型一部分实施例,而不是全部的实施例。基于本实用新型中的实施例,本领域普通技术人员在没有做出创造性劳动前提下所获得的所有其他实施例,都属于本实用新型保护的范围。
图1为本实用新型的第一个实施例之一,结合附图具体说明本实施例,包含有伸缩梁1、前梁2、顶梁3、护顶板4、斜梁5、上连杆6、下连杆7、底座8、左伸缩立柱9、推移伸缩缸10、右伸缩立柱16、前梁伸缩缸12、推动伸缩缸13、护顶伸缩缸14和立柱护板15,
在顶梁3和底座8之间设置有左伸缩立柱9和右伸缩立柱16并且在底座8的侧面部上设置有立柱护板15,在立柱护板15上设置有上连杆6和下连杆7并且在顶梁3和上连杆6之间、顶梁3和下连杆7之间设置有斜梁5,在底座8的端头设置有推移伸缩缸10,在顶梁3的侧面部设置有护顶板4并且在顶梁3与护顶板4之间设置有护顶伸缩缸14,在顶梁3的前端端面部设置有前梁2并且在顶梁3与前梁2之间设置有前梁伸缩缸12,在前梁2的前端端面部设置有伸缩梁1并且在前梁2与伸缩梁1之间设置有推动伸缩缸13。
在本实施例中,顶梁3设置为包含有箱部31、左连接耳32和右连接耳33并且左连接耳32和右连接耳33分别设置为与箱部31的端头联接,在箱部31的底端端面部分别设置有左销轴孔35和右销轴孔34并且在左连接耳32和右连接耳33上分别设置有插孔体37和铰接孔36,左销轴孔35设置为与左伸缩立柱9联接并且右销轴孔34设置为与右伸缩立柱16联接,插孔体37设置为与前梁2联接并且铰接孔36设置为与前梁伸缩缸12联接,护顶板4和护顶伸缩缸14分别设置为与箱部31的侧面部转动式联接,箱部31设置为矩形箱状体并且左连接耳32和右连接耳33分别设置为双耳状体,左销轴孔35、右销轴孔34、插孔体37和铰接孔36分别设置为圆形孔并且左销轴孔35和右销轴孔34分别设置为沉入在箱部31中。
通过顶梁3,形成了对前梁2、前梁伸缩缸12、护顶板4、护顶伸缩缸14、左伸缩立柱9和右伸缩立柱16的支撑连接点,由插孔体37,实现了与前梁2的转动连接,由铰接孔36,实现了与前梁伸缩缸12的转动连接,由左销轴孔35,实现了与左伸缩立柱9的转动连接,由右销轴孔34,实现了与右伸缩立柱16的转动连接,由箱部31,实现了与护顶板4的转动连接,实现了与护顶伸缩缸14的转动连接,由左连接耳32和右连接耳33,实现了前梁2的左右连接点。
在本实施例中,底座8设置为船形体并且底座8设置为包含有底板部81、左后侧板部82和右前侧板部83,在底板部81的侧面部的左端部分别设置有左后侧板部82并且在底板部81的侧面部的右端部分别设置有右前侧板部83,在左后侧板部82和右前侧板部83之间设置有立柱护板15并且右伸缩立柱16和推移伸缩缸10分别设置为与右前侧板部83铰接式联接,底板部81设置为U字形板状体并且底板部81的左右端头设置为向上呈锐角延伸分布,左后侧板部82的端头和右前侧板部83的端头分别设置为具有向外延伸的拐角板状体。
通过底座8,形成了对推移伸缩缸10、右伸缩立柱16和立柱护板15的支撑连接点,由右前侧板部83,实现了与右伸缩立柱16的连接,实现了与推移伸缩缸10的连接,由左后侧板部82,实现了与立柱护板15的转动连接,由底板部81,实现了与底座8和地基的接触连接。
在本实施例中,立柱护板15设置为直角梯形板状体并且在立柱护板15上分别设置有左连接孔151、右上连接孔152和右下连接孔153,左连接孔151设置为与上连杆6联接并且右上连接孔152设置为与下连杆7联接,立柱护板15设置为镶嵌在底座8中并且左连接孔151、右上连接孔152和右下连接孔153分别设置为圆形孔,左伸缩立柱9设置为与立柱护板15铰接式联接。
通过立柱护板15,形成了对上连杆6、下连杆7、底座8和左伸缩立柱9的支撑连接点,由立柱护板15,实现了与底座8的连接,实现了与左伸缩立柱9的连接,由左连接孔151,实现了与上连杆6的转动连接,由右上连接孔152,实现了与下连杆7的转动连接,由右下连接孔153,实现了与吊装钩的连接。
在本实施例中,左伸缩立柱9和右伸缩立柱16设置为三节式伸缩缸并且左伸缩立柱9的上端端头的转动轴和右伸缩立柱16的上端端头的转动轴分别设置为与顶梁3串接式联接并且左伸缩立柱9的下端端头的转动轴和右伸缩立柱16的下端端头的转动轴分别设置为与底座8联接,左伸缩立柱9的竖向中心线与右伸缩立柱16的竖向中心线之间的夹角设置为19-23°,左伸缩立柱9的竖向中心线与底座8的竖向中心线之间的夹角设置为8-10°并且右伸缩立柱16的竖向中心线与底座8的竖向中心线之间的夹角设置为11-13°,左伸缩立柱9和右伸缩立柱16分别设置为沿顶梁3的横向中心线间隔排列分布。
通过左伸缩立柱9和右伸缩立柱16,形成了对顶梁3和底座8的支撑连接点,由左伸缩立柱9和右伸缩立柱16,实现了与底座8的连接,实现了与顶梁3的连接。
在本实施例中,斜梁5设置为梯形板状体并且在斜梁5的前端头设置有第一铰接孔部51,在斜梁5的后端头设置有第二铰接孔部52和第三铰接孔部53并且第二铰接孔部52和第三铰接孔部53设置为呈间隔排列分布,第一铰接孔部51设置为与顶梁3联接并且第二铰接孔部52设置为与上连杆6联接,第三铰接孔部53设置为与下连杆7联接,第一铰接孔部51、第二铰接孔部52和第三铰接孔部53分别设置为圆形孔。
通过斜梁5,形成了对顶梁3、上连杆6和下连杆7的支撑连接点,由第一铰接孔部51,实现了与顶梁3的连接,由第二铰接孔部52,实现了与上连杆6的连接,由第三铰接孔部53,实现了与下连杆7的连接。
在本实施例中,上连杆6和下连杆7分别设置为矩形条状体并且上连杆6的一个端头和下连杆7的一个端头分别设置为与立柱护板15铰接式联接,上连杆6的另一个端头和下连杆7的另一个端头分别设置为与斜梁5铰接式联接并且上连杆6与下连杆7设置为呈相互平行排列分布。
通过上连杆6和下连杆7,形成了对斜梁5和底座8的支撑连接点,由上连杆6和下连杆7,实现了与斜梁5的连接,实现了与底座8的连接。
在本实施例中,推移伸缩缸10设置为两节式伸缩缸并且推移伸缩缸10设置为通过连接钩与底座8联接。
通过推移伸缩缸10,形成了对底座8的支撑连接点,由推移伸缩缸10,实现了与底座8的牵引连接。
在本实施例中,前梁2设置为箱状体并且在前梁2的左端头设置有连接耳部,在前梁2的右端头设置有容纳腔体并且伸缩梁1设置在前梁2的容纳腔体中,前梁2的连接耳部设置为与顶梁3联接并且前梁伸缩缸12设置为与前梁2的下端端面部联接。
通过前梁2,形成了对伸缩梁1、伸缩梁1和前梁伸缩缸12的支撑连接点,由前梁2,实现了与伸缩梁1的滑动连接,实现了与前梁2的连接,实现了与前梁伸缩缸12的连接。
在本实施例中,伸缩梁1设置为矩形板状体并且在伸缩梁1的中间部设置有连接耳部,伸缩梁1设置为与前梁2插接式联接并且推动伸缩缸13设置为与伸缩梁1的连接耳部铰接式联接。
通过伸缩梁1,形成了对前梁2和推动伸缩缸13的支撑连接点,由伸缩梁1,实现了与前梁2的滑动连接,实现了与推动伸缩缸13的连接。
在本实施例中,护顶板4设置为矩形板状体并且护顶板4设置为通过销轴与顶梁3翻转式联接,护顶伸缩缸14设置为与护顶板4的下端端面部铰接式联接。
通过护顶板4,形成了对顶梁3和护顶伸缩缸14的支撑连接点,由护顶板4,实现了与顶梁3的连接,实现了与护顶伸缩缸14的连接。
在本实施例中,前梁伸缩缸12、推动伸缩缸13和护顶伸缩缸14分别设置为两节式伸缩缸,前梁伸缩缸12的一个端头设置为通过销轴与顶梁3联接并且前梁伸缩缸12的另一个端头设置为通过销轴与前梁2联接,推动伸缩缸13的一个端头设置为通过销轴与前梁2联接并且推动伸缩缸13的另一个端头设置为通过销轴与伸缩梁1联接,护顶伸缩缸14的一个端头设置为通过销轴与顶梁3联接并且护顶伸缩缸14的另一个端头设置为通过销轴与护顶板4联接。
通过前梁伸缩缸12,形成了对顶梁3和前梁2的支撑连接点,由前梁伸缩缸12,实现了与顶梁3的连接,实现了与前梁2的推力连接,通过推动伸缩缸13,形成了对前梁2和伸缩梁1的支撑连接点,由推动伸缩缸13,实现了与前梁2的连接,实现了与伸缩梁1的推力连接,通过护顶伸缩缸14,形成了对顶梁3和护顶板4的支撑连接点,由护顶伸缩缸14,实现了与顶梁3的连接,实现了与护顶板4的推力连接。
在本实施例中,顶梁3和底座8与左伸缩立柱9和右伸缩立柱16设置为按照呈V字形支撑的方式分布并且顶梁3、底座8、左伸缩立柱9和右伸缩立柱16与立柱护板15、斜梁5、上连杆6和下连杆7设置为按照侧支撑护栏的方式分布,顶梁3与伸缩梁1、前梁2、护顶板4、前梁伸缩缸12、推动伸缩缸13和护顶伸缩缸14设置为按照全方位扩展延伸的方式分布并且伸缩梁1的中心线、前梁2中心线、顶梁3中心线、底座8中心线、前梁伸缩缸12中心线和推动伸缩缸13中心线设置在同一条直线上,一个立柱护板15、一个斜梁5、一个上连杆6和一个下连杆7设置为组成一组侧支撑护栏部件并且两组侧支撑护栏部件分别设置在顶梁3和底座8之间的侧面部。
通过推移伸缩缸10,带动底座8移动,把底座8固定在煤矿需要支护的位置,启动左伸缩立柱9和右伸缩立柱16伸长,对顶梁3产生推升,把顶梁3固定在支护顶部,通过前梁伸缩缸12,把前梁2展开,通过护顶伸缩缸14,把护顶板4展开,通过推动伸缩缸13,把伸缩梁1展开,同时斜梁5与上连杆6和下连杆7转动,从而使斜梁5与上连杆6和下连杆7展开,通过对左伸缩立柱9和右伸缩立柱16的伸缩量的调整,实现对顶梁3支护位置的调节,通过对前梁伸缩缸12的伸缩量的调整,实现对前梁2支护位置的调节,通过对护顶伸缩缸14的伸缩量的调整,实现对护顶板4支护位置的调节,通过对推动伸缩缸13的伸缩量的调整,实现对伸缩梁1支护位置的调节,当支护完毕后,左伸缩立柱9和右伸缩立柱16收缩,带动顶梁3与底座8合拢,通过前梁伸缩缸12,把前梁2收拢,通过护顶伸缩缸14,把护顶板4收拢,通过推动伸缩缸13,把伸缩梁1收缩。
在本实施例中,左伸缩立柱9的竖向中心线与右伸缩立柱16的竖向中心线之间的夹角设置为19-23°,左伸缩立柱9的竖向中心线与底座8的竖向中心线之间的夹角设置为8-10°并且右伸缩立柱16的竖向中心线与底座8的竖向中心线之间的夹角设置为11-13°,相邻的两个伸缩立柱之间的夹角设置为19-23°的伸缩立柱组。
本实用新型的第一个实施例之二,左伸缩立柱9的竖向中心线与右伸缩立柱16的竖向中心线之间的夹角设置为19°,左伸缩立柱9的竖向中心线与底座8的竖向中心线之间的夹角设置为8°并且右伸缩立柱16的竖向中心线与底座8的竖向中心线之间的夹角设置为11°,相邻的两个伸缩立柱之间的夹角设置为19°的伸缩立柱组。
本实用新型的第一个实施例之三,左伸缩立柱9的竖向中心线与右伸缩立柱16的竖向中心线之间的夹角设置为23°,左伸缩立柱9的竖向中心线与底座8的竖向中心线之间的夹角设置为10°并且右伸缩立柱16的竖向中心线与底座8的竖向中心线之间的夹角设置为13°,相邻的两个伸缩立柱之间的夹角设置为23°的伸缩立柱组。
本实用新型的第一个实施例之四,左伸缩立柱9的竖向中心线与右伸缩立柱16的竖向中心线之间的夹角设置为21°,左伸缩立柱9的竖向中心线与底座8的竖向中心线之间的夹角设置为9°并且右伸缩立柱16的竖向中心线与底座8的竖向中心线之间的夹角设置为12°,相邻的两个伸缩立柱之间的夹角设置为21°的伸缩立柱组。
本实用新型的第二个实施例,还包含有横向连接头41和连架收缩缸11并且横向连接头41的一个端头设置为与底座8联接,连架收缩缸11设置在相邻的两个横向连接头41的另一个端头之间。
在本实施例中,在横向连接头41的一个端头设置有通孔部并且在横向连接头41的另一个端头设置有叉口部,横向连接头41的通孔部设置为通过销轴与底座8铰接式联接并且横向连接头41的叉口部设置为通过销轴与连架收缩缸11铰接式联接,横向连接头41设置为沿底座8的横向中心线间隔排列分布。
通过横向连接头41,形成了对底座8和连架收缩缸11的支撑连接点,由横向连接头41,实现了与底座8的连接,实现了与连架收缩缸11的连接,实现了对相邻的底座8的连接。
在本实施例中,连架收缩缸11设置为具有双头伸缩部的三节伸缩缸并且连架收缩缸11的伸缩头设置为通过销轴与横向连接头41联接。
通过连架收缩缸11,形成了对横向连接头41的支撑连接点,由连架收缩缸11,实现了与横向连接头41的连接,实现了对相邻的底座8的连接,
把横向连接头41与底座8连接,由连架收缩缸11通过横向连接头41,把相邻的底座8的连接在一起,通过连架收缩缸11的伸缩量的调整,实现对底座8支护位置的调节。
本实用新型的第三个实施例,还包含有竖向连接头18和连架收缩缸11并且竖向连接头18的一个端头设置为与顶梁3联接,连架收缩缸11设置在相邻的两个竖向连接头18的另一个端头之间并且连接头18的另一个端头设置为与左伸缩立柱9的上端端头联接。
在本实施例中,在竖向连接头18的端头分别设置有通孔部并且竖向连接头18的上端端头的通孔部分别设置为通过销轴与顶梁3铰接式联接,竖向连接头18的下端端头的通孔部分别设置为通过销轴与左伸缩立柱9和连架收缩缸11铰接式联接,竖向连接头18设置为沿顶梁3的横向中心线间隔排列分布。
通过竖向连接头18,形成了对顶梁3和连架收缩缸11的支撑连接点,由竖向连接头18,实现了与顶梁3的连接,实现了与连架收缩缸11的连接,实现了对相邻的顶梁3的连接。
在本实施例中,连架收缩缸11设置为具有双头伸缩部的三节伸缩缸并且连架收缩缸11的伸缩头设置为通过销轴与竖向连接头18联接。
通过连架收缩缸11,形成了对竖向连接头18的支撑连接点,由连架收缩缸11,实现了与竖向连接头18的连接,实现了对相邻的底座8的连接,
把竖向连接头18与顶梁3连接,由连架收缩缸11通过竖向连接头18,把相邻的顶梁3的连接在一起,通过连架收缩缸11的伸缩量的调整,实现对顶梁3支护位置的横向调节。
本实用新型的第四个实施例,按照形成前后平衡支撑点的方式把用于地面支撑的底座8、用于顶面支撑的支撑板装置和具有至少两个伸缩立柱的伸缩立柱组相互联接。
在本实施例中,按照沿底座8的竖向中心线向外倾斜的方式把伸缩立柱组与底座8和支撑板装置联接。
本实用新型的第二、三和四个实施例是以第一个实施例为基础。
本实用新型具有下特点:
1、由于设计了底座8、支撑板装置和伸缩立柱组,通过底座8,形成地面支撑,通过支撑板装置,形成顶面支撑,通过伸缩立柱组的伸缩立柱的伸缩量的调节,对支撑板装置的位置进行复位调节,防止顶面支撑出现偏移,不再使用单个的伸缩立柱,因此提高了超前液压支架装置的可靠性能。
2、由于设计了推移伸缩缸10,实现了对超前液压支架装置连架的移动。
3、由于设计了斜梁5、上连杆6、下连杆7和立柱护板15,实现了对顶梁3的支撑,实现了对左伸缩立柱9和右伸缩立柱16的保护。
4、由于设计了伸缩梁1、前梁2、顶梁3、护顶板4、前梁伸缩缸12、推动伸缩缸13和护顶伸缩缸14,增大了顶面的支护面积。
5、由于设计了横向连接头41、竖向连接头18和连架收缩缸11,实现了对超前液压支架装置连架的横向位置的调节,防止顶梁3出现偏移。
6、由于设计了对结构形状进行了数值范围的限定,使数值范围为本实用新型的技术方案中的技术特征,不是通过公式计算或通过有限次试验得出的技术特征,试验表明该数值范围的技术特征取得了很好的技术效果。
7、由于设计了本实用新型的技术特征,在技术特征的单独和相互之间的集合的作用,通过试验表明,本实用新型的各项性能指标为现有的各项性能指标的至少为1.7倍,通过评估具有很好的市场价值。
还有其它的形成前后平衡支撑点的底座8、支撑板装置和伸缩立柱组联接的技术特征都是本实用新型的实施例之一,并且以上所述实施例的各技术特征可以进行任意的组合,为满足专利法、专利实施细则和审查指南的要求,不再对上述实施例中的各个技术特征所有可能的组合的实施例都进行描述。
因此在内,凡是包含有设置在支护点的地基上的底座8、设置在支护点的顶面上的支撑板装置、设置在底座8和支撑板装置之间并且相邻的两个伸缩立柱之间的夹角设置为19-23°的伸缩立柱组的技术内容都在本实用新型的保护范围内。